Spray Polyurethane Foam (SPF) roofing is one of the most advanced commercial roofing systems available today because If its versatility, durability and cost-competitive characteristics. SPF roofs differ from contemporary commercial roofing options because it is manufactured by the applicator on the job-site and fabricated to self-flash perfectly to the contour of a building, rather than cut into many pieces and mechanically attached. Most importantly, because it is spray applied, it forms a seamless and monolithic barrier that will not allow air and water infiltration.
Can I use spray foam over my existing commercial roof?
A spray applied roofing system is a great option to restore an existing flat roof system. With that said, not all existing roofs are candidates for an SPF roof restoration. In order to install a high performance sprayed-in-place system that is adhered to the substrate, seamless, lightweight, and self-flashing, the application and workmanship must be premium quality. In addition, the SPF applicator must have detailed information on the type and condition of the existing roof. If any one of the restrictions are not met, then the new foam roof may not perform as expected.
Prior to the application of any spray polyurethane foam, the roof surface must be inspected. The intended purpose: to insure that the surface is is clean and in condition to allow the SPF to properly adhere to the existing roofing material. The following must be met to determine suitable SPF roof application over an existing roof:
Commercial Roof Surface Inspection for SPF Application:
There are two general principles that must be met while screening an existing commercial flat roof for compatibility of an SPF roof restoration:
- Core samples must be taken to identify potential moisture saturated areas underneath the existing roofing system. A roofing system that is saturated with water 25% or more will generally result in a complete tear-off and reroof. Accurate moisture readings can be attained through the use of MDP strips.
- Core samples must be taken to identify structural characteristics of the assembly below the existing roof. The deck should be examined for rot, corrosion, and other deterioration. Any weak areas must be repaired. In some instances, a complete tear-off may be necessary to achieve a code-compliant and safe product for the client and the occupants of the building.
Once those two tasks have been met, the applicator may proceed.
Membrane Roofs:
All loose aggregate, dirt, debris, grease, and oil must be removed from the existing roof surface by power-broom, hydro-vacuum, or other appropriate means. Loose membrane seams and other openings must be mechanically secured but may be left air and water vapor permeable. Loose, damaged, and deteriorated flashings, details, and equipment must be repaired, secured, or removed.
Membrane blisters must be split and then secured. Loosed-laid membranes must be removed and secured by being overlaid with mechanically fastened board.
Wood Surfaces:
Plywood should be exterior grade (Type "X") not less than 15/32" thick, attached securely in place. The attachment must meet building code requirements fore resistance to wind uplift. The wood cannot contain more than 18% water, as measured in accordance with ASTM D 444-84, or ASTM D 4442-84.
Tongue and Groove, Sheathing, or Planking must be overlaid with a minimum 1/4" thick exterior grade plywood or suitable covering due to the possibility of variable openings and effects of aging and shrinking.
Prior to the application of a primer, all loose dirt and debris must be removed by using compressed air, vacuum, or broom. (Not washed with water.)
Wood decks should be primed with the foam manufacturer's approved primer to achieve optimal adhesion. The primer should be applied as soon as the wood deck is installed to resist any additional moisture pick-up between the time of installation and SPF application.
Metal Roof Surfaces:
Flat structural metal roof decks shall not be lighter than 22 gauge. A pitched metal building roof panel should not be lighter than 29 gauge, with a pitch of 1/4" in 12".
All joints should be correctly lapped, sealed, and fastened. If the metal surface is free of loose scale, rust, weathered or chalking paint, the applicator can remove loose dirt using compressed air, power wash, vacuum, or broom. Grease, oil, and other contaminates must be removed with proper cleaning solutions.
Fluted metal roof decks require a suitable method of covering or filling the flutes prior to SPF application to achieve a smoother more uniform surface. With the EnduraRock foam and gravel roof, a mesh fabric may be rolled-out across the roof deck, spanning the flutes, and pulled taut to the roof deck.
Concrete Roof Surfaces:
In all cases, concrete roof surfaces should be free of laitance and chemical release agents. The applicator must remove loose dirt, dust, and debris by using compressed air, vacuum, or broom. Oil, grease, form release agents or other contaminates should be removed by proper leaning solutions. It is recommended that all concrete surfaces by primed with a concrete primer recommended by the SPF manufacturer.
Roof deck joints and openings exceeding 1/4" should be grouted or caulked and allowed to cure prior to SPF application. Also, concrete must be allowed to cure at least 28 days prior to the application.
Built Up Roofing (BUR):
Built Up Roofing (BUR) is a roofing membrane consisting of alternative applications of bituminous impregnated felt and hot (or cold) mopped bitumen. The surface can be flood-coated with bitumen and embedded with crushed slag or gravel.
Prior to SPF application, all loose gravel, dust, and debris must be removed by using a vacuum, power broom, or compressed air. A wet-vacuum may also be used if suitable drying time is allowed before the SPF application.
The roof must be thoroughly inspected or tested to determine if moisture is present within the BUR assembly. Saturated insulation must be removed and replaced with compatible materials. The existing roof should also be inspected for proper adhesion between layers of BUR felts, the insulation, and the deck. Areas of poor adhesion can be mechanically fastened. Blisters, wrinkles, buckles, and fish-mouths should be cut-out or securely fastened.
Remove or refasten all soft mastic, asphaltic materials, loos flashing, loose counterflashing, and gravel stops as required.
Spray Polyurethane Foam (SPF) Roofs:
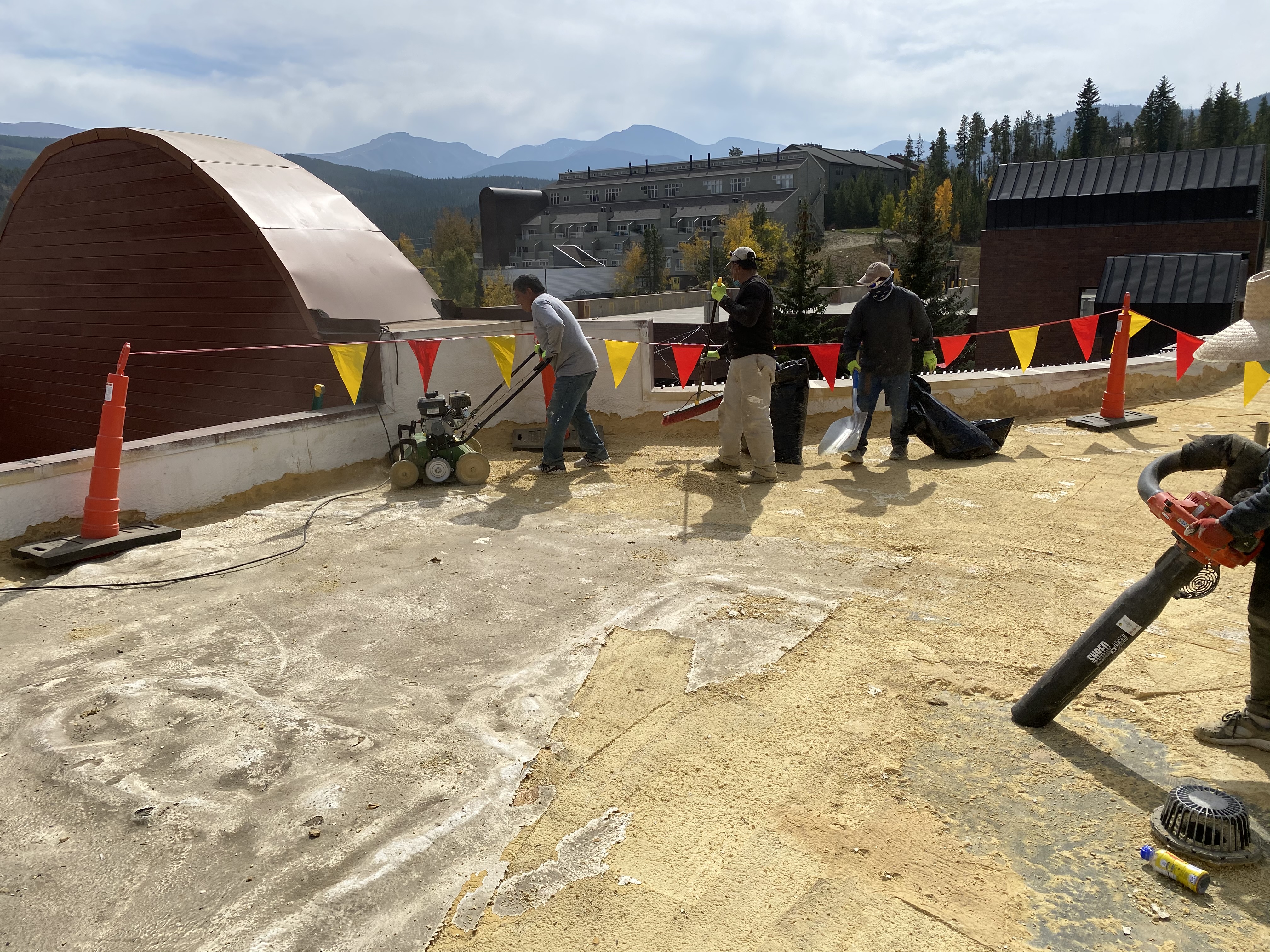
Existing SPF roofing systems can be can be recovered in most instances. The applicator must scarify off the top layer of the existing foam roof until well-adhered closed-cell foam is exposed. MDP strips can then be used to determine if moisture is present in existing foam. Depending on the amount of saturation, if applicable, the foam can be completely removed and taken down to dry deck or allowed to dry (if Mother Nature allows time). All loose dust, foam, and debris must be removed by compressed air, vacuum, or brooms. New foam can then be applied to the dry scarified foam surface. Each pass thickness should be a minimum of 1/2" and the full thickness of the foam should be applied to the respective roof section within the same day.
Titan Applicators has been serving Colorado commercial building owners and real estate managers since 2015. Our team of experienced, professional, and skilled spray foam applicators is highly competent in the application of spray polyurethane foam roofing and roof coatings. Our products speak for themselves by saving building owners time and money through sustainability, ease of application, durability, and ease of maintenance.
Call today to speak with one of our friendly reps!