Single Ply roofing systems are popular flat-roof and low-slop roofs on commercial buildings here in Colorado because the options, styles, and technologies have gradually improved in recent history. Compared to traditional multi-layered flat roofing systems, such as Asphalt Roofs (BUR), Styrene Butadiene Styrene (SBS) roofs, or Atactic Polypropylene (APP) roofs, these roofing systems increased in acceptance because they reduced installation times, material costs were lowered, and required less man-power to install.
The three most popular types of Single-Ply commercial roofs are: PVC, TPO & EPDM.
EPDM - “Ethylene Propylene Diene Monomer”
Also known as “rubber roofing,” EPDM grew in popularity in the 1960’s as a more cost effective and easier system to lay down than the traditional asphalt or BUR systems. It has a very similar feel to rubber and is typically black in color. One of the benefits of the EPDM roofing material is that it is highly UV stable due to the carbon black raw materials
PVC - “Polyvinyl Chloride”
Also referred to as a “vinyl roof,” the two main raw materials in PVC roof are ethylene and coloring. A PVC roofing system consists of two layers of PVC membrane material covering a reinforced scrim. The top layer is supposed to be UV resistant and flexible. The bottom ply membrane typically consists of more plasticizers for increased flexibility and weldability.
TPO - “Thermoplastic Polyolefin”
Since its inception in the 1980s, standard TPO roofs have a cap and core membrane with a reinforced scrim sandwiched between the two layers. Like other single-ply roofing systems, the increase in technological improvements has increased the strength, and popularity, of TPO roofs over time,
What Is the Life Expectancy Of A Single-Ply Roof?
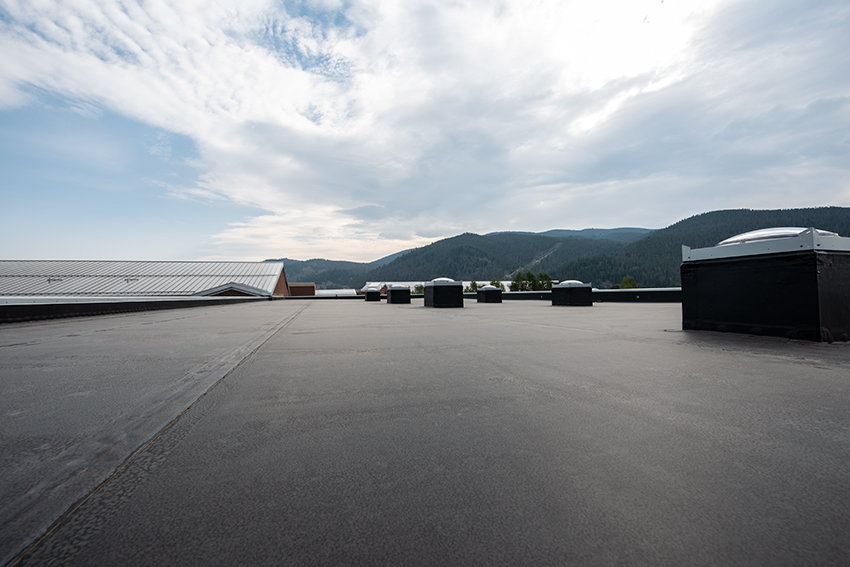
All roofing systems are put under unique third-party testing. But, what should a commercial building owner expect from a membrane roof here in Colorado? From our experience, the majority of flat-roof membranes can last around 25 years under perfect conditions. Perfect conditions consist of a high quality installation and a well executed semi-annual maintenance plan.
Unfortunately, there are many commercial roofing contractors lurking in the shadows of the industry that get outside of their wheel-house and install single-ply roofing membranes that they aren’t familiar with and not to specifications. Any roofing contractor, regardless of her or his experience, should install a single-ply roof on a commercial flat roof under the consultation and guidance from the membrane manufacturer. Things such as roof design, building code, building use, and climate zone will all play a role in the product specs and installation methods vis-a-vis life expectancy of the roof.
What To Do If You Have A Roof Leak?
It is our experience that single-ply roof leaks occur most commonly in the following locations:
The Seams
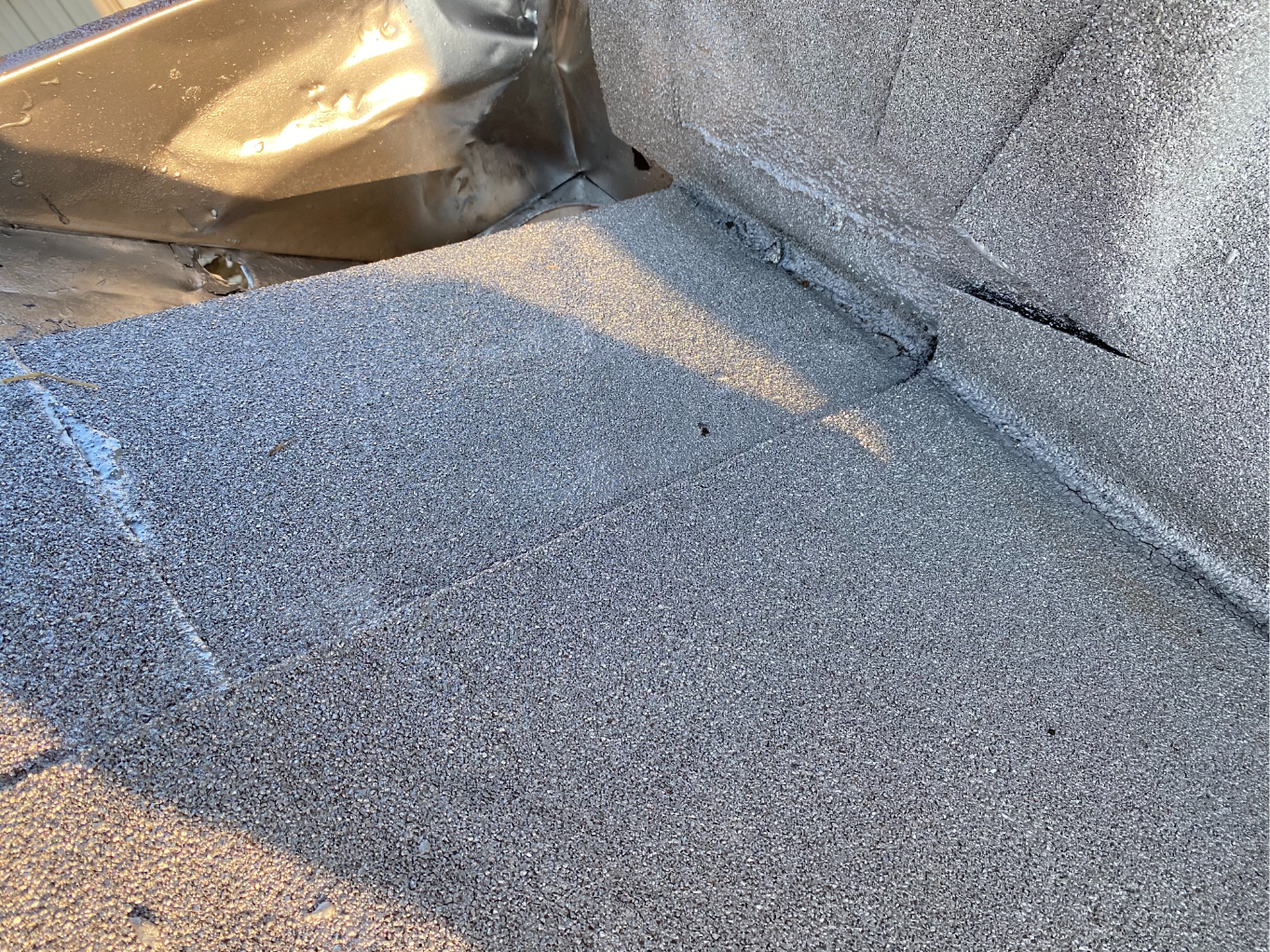
One of the downfalls of flat roofing membranes is that they are made of many separate pieces that must be puzzled together, overlapped, and sealed properly at the seams. Unfortunately, these seams can create some issues. They are the first spots to weaken and the first spots to fail, which leaves the opportunity for water to enter your building.
The Colorado weather throws rain, sleet, hail, snow, wind, sun and freezing temperatures at the roof each and every year. Regardless of how they are bonded, the seam begin to lose adhesion to one another and gradually rip farther and farther apart. Once water penetrates the membrane, not only does it enter your building but it begins to saturate the insulation. This saturation kills your building’s energy performance and holds water in place leading to potential wood rot and structural damage.
The Penetrations
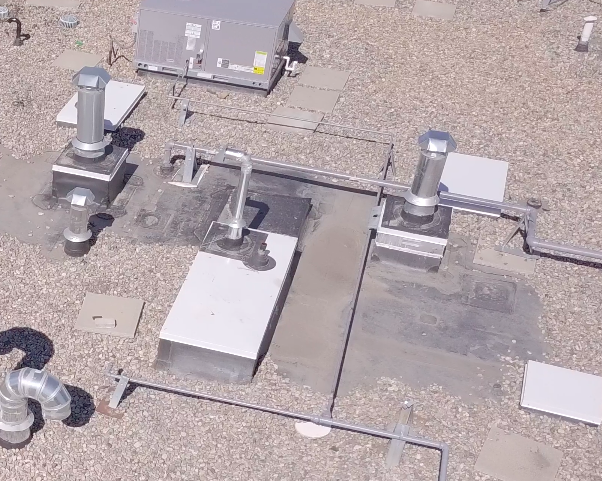
What is a roof penetration? We’re glad you asked! Roof penetrations include, but are not limited to, HVAC units, pipes, exhausts, hood vents, skylights, conduit, and flashings.
Why do those matter? Because the roofing membrane needs to fit tightly around those penetrating items in order to keep water out. Much like a bottle cap that isn’t tightly screwed-down, water can leak through the tiniest spaces around these penetrations. If flashings or boots aren’t installed properly, or if they begin to fail under stress, water will have open access to move freely into your building.
Roof Damage
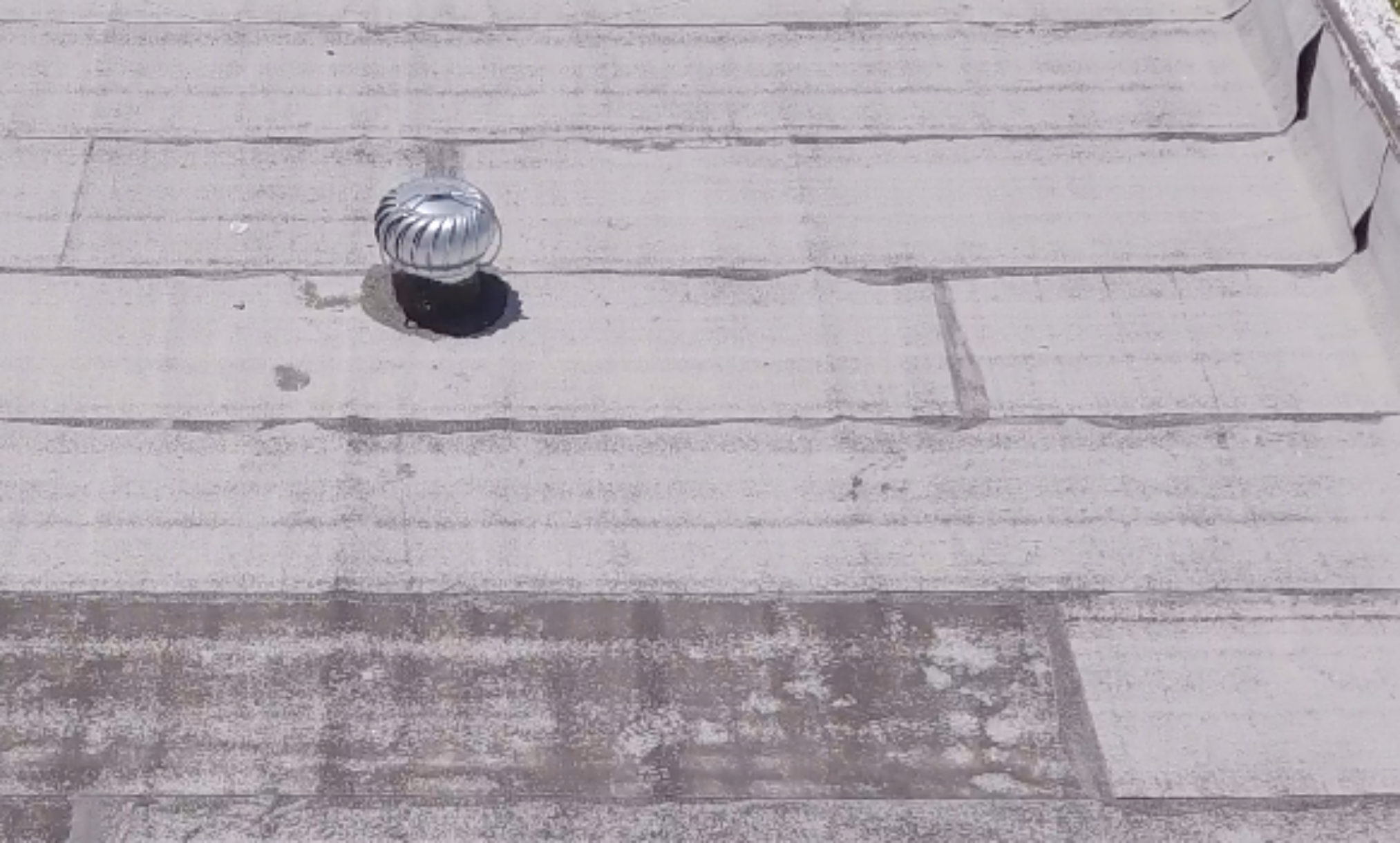
Punctures or tears to a single-ply roof can be the result of external forces like a downed tree and hail or third-party damage from another contractor working on top of the roof. Regardless of the source of a leak, once damage has occurred, it’s important to locate and fix that damage as soon as possible. That’s why implementing and executing a routine roof maintenance plan is of the utmost importance.
Poor Draining or Ponding Water
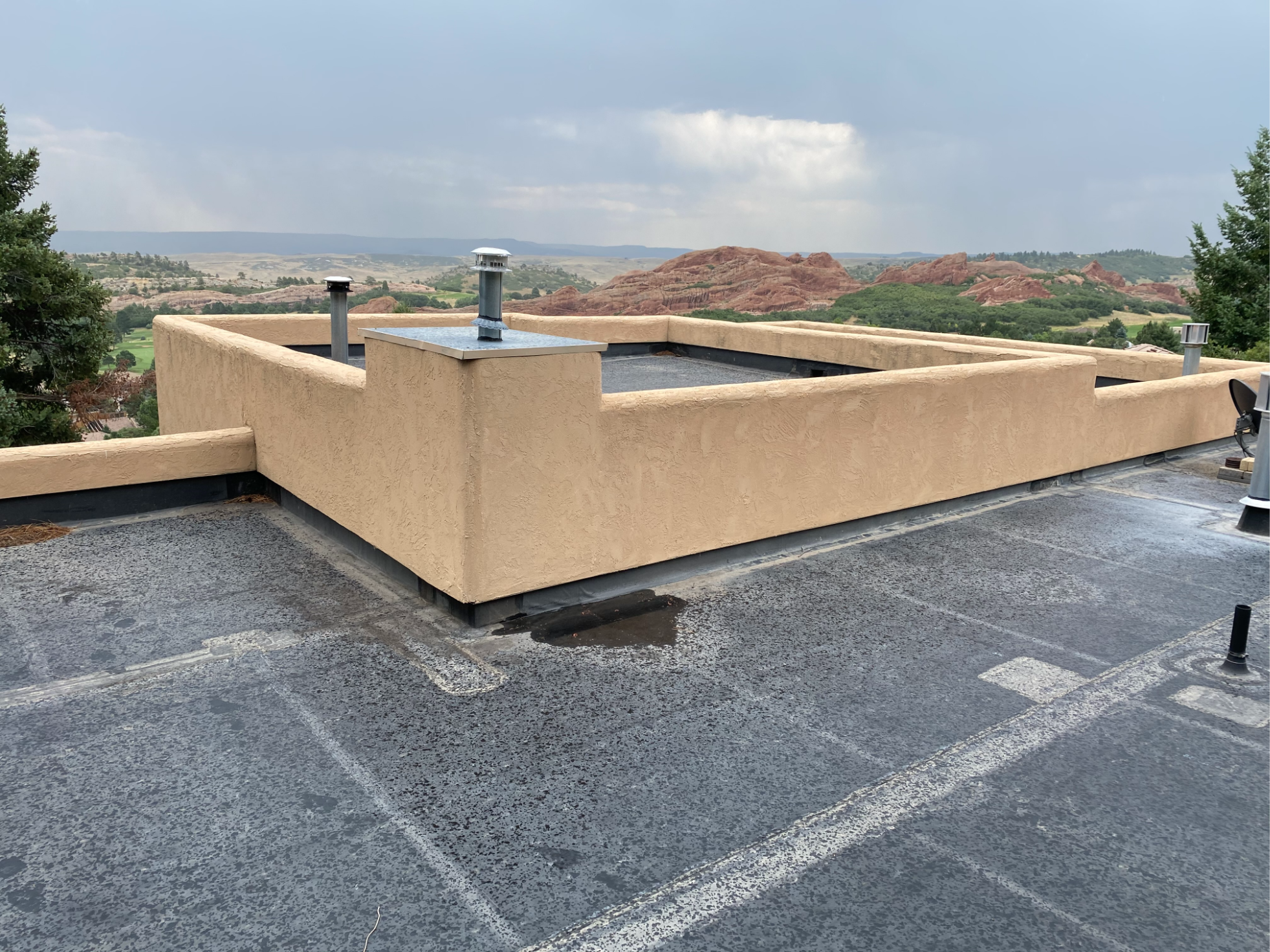
Standing water may not immediately result in a roof leak. But, if that water remains on a roof for long periods of time it will begin to wear-out the roofing membrane and create weak spots that may eventually result in a leak. Obvious signs of improper drainage or pooling water (other than actual standing water) are rings of dirt left being by evaporated water.
How To Restore A Single-Ply Roof
In some instances, commercial flat roof leaks can be remedied by simply patching them. On most occasions, patches will simply prolong the inevitable. That’s why Titan Applicators takes pride in offering commercial building owners and managers monolithic fluid-applied roof restoration options. They provide commercial real estate owners the option to cost effectively restore their existing single-ply roofing systems while avoiding high costs associated with a full tear-off.
Fluid-applied roof restorations include:
Spray Polyurethane Foam (SPF)
SPF roofing solutions can be used on any shape, configuration, or contour of a roof and can be used over most existing roofing systems. It is self flashing and monolithic, eliminating the chance of leaks at failing seams. The only thing more exciting that the ease of installation is the level of protection it provides to your building.
Silicone Coatings
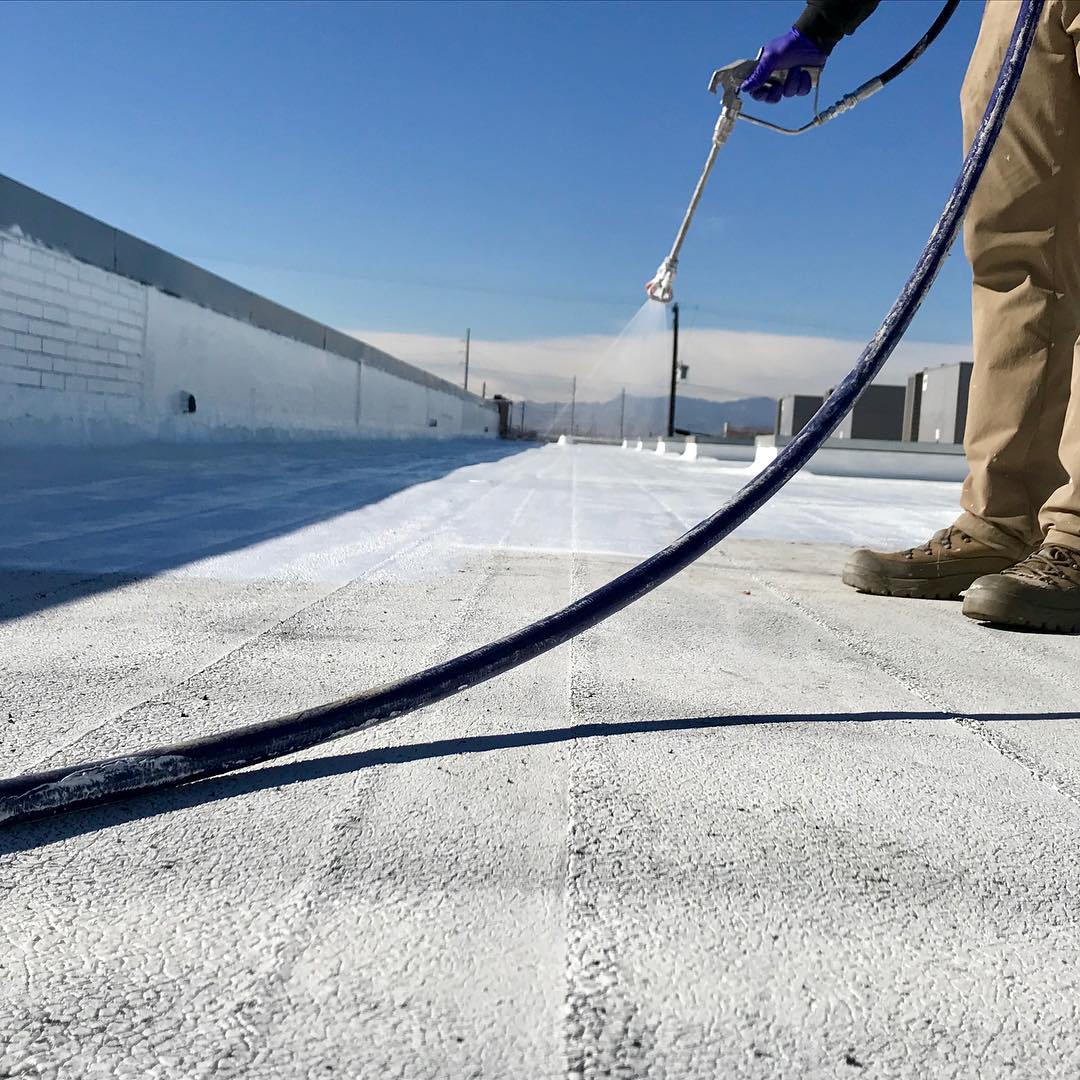
Silicone coatings help extend the life of single-ply roofing systems while simultaneously improving performance and reducing maintenance costs. They are easy to install and only require one coat, which minimizes disruption to facility operations. Furthermore, they create a monolithic barrier on top of your building that remains unaffected by standing water.
Acrylic Elastomeric Coatings
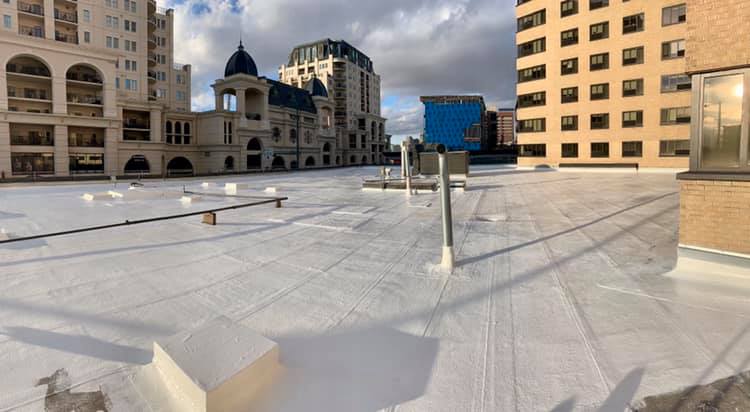
Acrylic elastomeric roof coatings can be used over most existing single-ply roofing systems. They are durable and possess excellent dirt pick-up resistance. Also, most importantly, that have great adhesion and allow building owners to hit the “reset button” on the life of their existing roofs, leaving them with a seamless and monolithic commercial roofing system.
Titan Applicators has helped hundreds of commercial building owners and real estate managers up and down the Front Range of Colorado by giving them cost-effective, practical, and long-lasting commercial roof restoration solutions.
Our flat roof spray foam & coating products can restore and extend the life of:
- TPO
- EPDM
- Metal
- Asphalt
- PVC
- SBS Granulated
- APP
- Modified Bitumen
- HypalomTM
- Concrete
Contact us today!